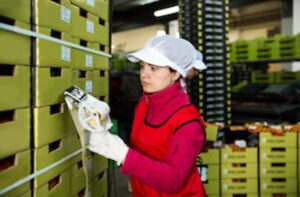
批次可追溯性对于消费者安全至关重要。虽然100%的时间不可能防止食品安全危险,但很多可追溯性允许制造商和经销商在发生时阻止污染的传播,并防止更多客户进入受污染物品。储存,处理和分配中的常见批次可追溯性问题可以使难以包含污染。寻找这些常见的批次可追溯性问题,并尝试这些解决方案来提高流程的安全性和安全性。
食品加工中批次溯源问题及解决方案
1.问题:测量不准确
解决方法:适当的校准,一致的条件
批次可追溯性的一个最重要的方面是准确性。当每种成分在配方中加入适量时,标签也会准确无误,任何成分都可以很容易地追溯到产品,反之亦然。当这些测量出错时,不仅会影响成品的质量,还会影响批量的可追溯性。
精确的测量需要一个精确的称重和配料系统。首先,在物料进入料斗或料仓时或刚刚进入之前称量是很有帮助的。许多供应商会把袋子装得太满,所以不会少找顾客钱,然而,装得太满可能会毁掉一个食谱。不要假设一个写着25公斤的袋子实际上是25公斤。额外的0.2或0.5公斤会严重破坏你的食谱,特别是对关键的配料。在过程的开始和整个过程中,一定要进行安装尺度和流量计具有适当的精度水平,并定期校准它们以确保它们保持准确。
除了称重设备的问题,其他情况也会导致不准确。例如,温度的变化,比如卡车和设备之间的温度变化,或者储存和使用之间的温度变化,会导致某些成分的密度发生变化,比如油。这将干扰流量计的测量。保持一致的温度可以防止这个问题。
2.问题:在存储中混合批次
解决方法:适当的储存清洁,机会罐
存储是另一个可能导致批量可追溯性问题的挑战。如果分开的批次在储存期间密切接触,污染的可能性就会扩散。这通常发生在筒仓或储罐储存期间。如果储罐或筒仓在批次之间没有适当地清洗,那么将它们分离是没有什么用处的。如果要在现有地块用完的时候储存新地块,可以使用一个二级储存容器或机会罐。如果你使用的是实验配方和短时间使用的食材,这也很有用。
3.问题:混合多余的成分
解决方案:处理
如果在完成批次时留下成分,则必须处理它们。将剩余的批次混合到下一个批次中可能会减少浪费,但它也可以进行准确的批次可追溯性。也许是1997年发生这种批次可追溯性问题的最着名的例子哈德逊食品。没有积极的截止,成分不断从一批到下一个批量移动。当发生大肠杆菌污染时,没有办法准确地追踪污染的批次。这导致历史上最大的召回,破坏了哈德森食品,并证明了保持众多单独的批判性重要性。
4.问题:不准确的标签
解决方案:系统集成
准确标记对于批次可追溯性至关重要。如果最终产品没有用正确的成分标记,批号和日期,那么如果不是不可能的话,难以召回。标签和食品加工系统之间的无缝通信可以帮助尽可能准确地实现此过程。当系统接收,分配和批量产品时,集成标签系统将跟踪这些活动中的每一个。
5.问题:不准确的报告
解决方案:检查
当称重,混合,批量和标签系统都无缝工作时,它可以轻松制作很多跟踪。但是,如果这个系统脱离同步,那么立即了解它非常重要。应进行检查和验证,以确保系统的每个部分正常地通信和报告。
6.问题:缺乏验证
解决方案:模拟召回
在食品加工线和供应链中可追溯性的最终试验是召回。希望,召回的需要永远不会出现。但是,如果它确实,每个工作人员都很重要,了解该过程。模拟召回允许您在供应链中测试和验证可追溯性。这将向您展示您的系统是否准确地报告批号并在食品处理操作中维护准确的记录。它还将显示如何轻松或困难 - 将特定地段隔离,并揭示可能需要更改的地方。
食品加工在可追溯性方面起着重要作用。当你能够验证哪些成分会进入你的食谱,它们来自哪里,何时到达,以及最终产品的去向时,你就可以对自己在必要时进行召回的能力充满信心。这不仅会保护你的产品的完整性,也会保护你的企业的良好信誉。